Getting the right material lifting for your daily operation will greatly benefit staff health and improve productivity in your warehousing or manufacturing setting. But to help your business, you will have to choose the right material lifting that fits your needs in your daily operation, or it will become a burden.
Whether buying or renting a material lifting, you will want to fully utilize it to boost your warehouse productivity. Each warehouse is unique in size, layout, and material handling requirements. Each business will have its own standard of procedure. Finding the right equipment to fit your daily operation can be challenging.
There are many factors to consider to get suitable material lifting for your business. It can involve a complex selection process when you are looking for one. We have an overview of what equipment can be adapted to suit specific tasks to help you find the right equipment.
Which Material Lifting Equipment Do You Need?
1. Nature of loads
One of the factors that you need to consider when getting material lifting equipment is the load the equipment can take. Each piece of equipment has a maximum load. You would want to avoid getting one with a very low maximum load when you have heavy loads to carry. For example, a vacuum lifting system is customized for lifting a specific load, such as bags, boxes, or sheets.
So before you get the equipment, take note of the typical load’s size, weight, and shape. Calculate the dimension if you are getting vacuum pumps. If you are getting a crane or hoist, consider the mounting structures which adapt to the heaviest loads plus a safety margin. Also, consider how the goods will be packed. Will it be in bags, drums, or pallets?
You will also need to consider the nature of the material surface, such as wood, textile, or metal. Also, ask yourself if the materials are sensitive. Some facilities, such as food processing industries or pharmaceuticals, have strict hygiene requirements. These industries will usually opt for stainless steel material lifting equipment, which is easy to clean. Check if your materials are hazardous. If you are handling hazardous materials in a potentially explosive environment, you will want to get one that does not risk causing sparks.
2. Worker Safety
Accidents can happen in the workplace, but it can also be avoided. It is important to keep the staff safe, happy, and healthy. When selecting the equipment, you will want to consider minimizing the risk. It can reduce the health effects due to poor ergonomics.
Manual handling procedures are usually the root cause of accidents, which can be prevented. Even if the tasks are assisted by material lifting equipment, there will still be risks associated, such as repetitive stress injuries. Vacuum lifters are one of the effective ways to improve safety and mitigate health risks. But you will need to ensure that staff is trained to handle the equipment correctly.
3. Space Requirements
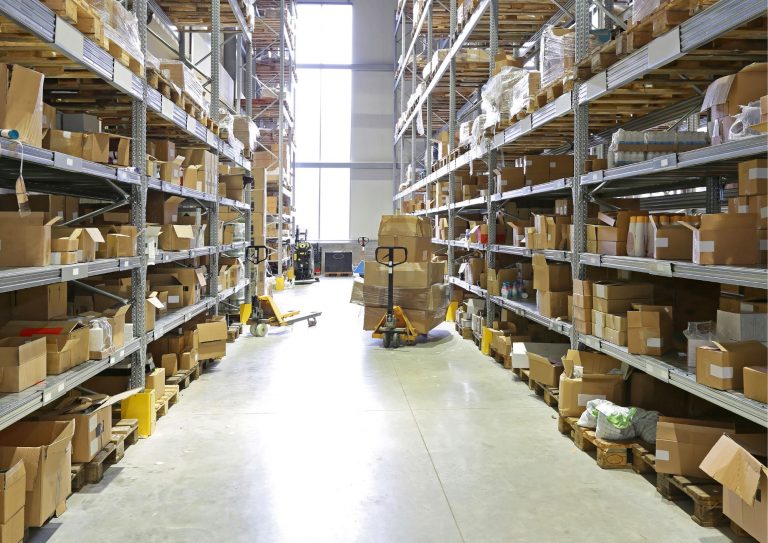
To fully utilize the material lifting equipment, you want to ensure enough space in your workplace. You’ll want to align the area as smoothly as possible. This includes considering the radius of cranes, required reach, height and width limitations, and maneuverability. Suppose you get mobile electric material liftings equipment, such as lifting trolleys or mobile order pickers. In that case, it doesn’t occupy much space, but you need to ensure charging points are available.
4. Traffic Patterns And Picking Processes
The flow of goods between the point of delivery and storage racks is important in the facility as it will affect productivity. Consider the volume of goods on average. Some material lifting equipment is designed for fast lifting, which can help to improve productivity when you have a high volume of lighter loads.
You will also want to consider the most efficient method and route to transport the goods to and from the storage. When loading the goods, consider if it needs to be turned or tilted in the lifting process. Or do you need to grip it from the side? You will want to get one that meets these requirements. Also, consider mobility and flexibility. It can help to save time and effort.
How to Select A Telehandler
Telehandlers are one of the common material lifting equipment used in warehouses. It can lift more and reach higher compared to a forklift. Telehandlers can be a cost-effective alternative to a crane, but it must depend on the capacity and lift height demands.
Telehandlers are mounted on a four-wheel drive chassis with a telescopic boom that allows them to reach upward and forward. You can consider getting a few different attachments for the end of a telehandler. You can add a pallet fork if you want something similar to a forklift. Other common attachments include platforms, lifting jibs, and buckets.
Besides the standard telehandlers, you can also find compact telehandlers in the market. Compact telehandlers are smaller and weigh less. It will be easier to maneuver and transport. Since it is smaller, the capacity and the lift height will be lesser. But it may need to be able to fit and navigate in small spaces due to the size.
How to Select A Crane System
There are many ways to configure a crane system to meet your material handling requirements. Different types of overhead bridge cranes and jib cranes can be found in warehousing and manufacturing settings. Depending on the shape and weight of the intended loads, cranes are complemented with wire or chain hoists and vacuum lifters. There are a few restrictions on the goods types that cranes can lift.
If you are opting for a jib crane, it allows for flexible movement within a space limited by arm length. An articulating jib crane can lift goods weighing up to 175 lbs for improved flexibility and reach in restricted areas. Stainless steel models can lift up to 2,200 lbs.
For those that need to cover extensive spaces or transport goods along specific paths, overhead cranes can be a good choice. Crane systems are custom solutions that can be built to suit the requirements of your facility. If you are considering getting a crane, it is best to consider it at the planning stage. It can get complicated in the future, so you will have to ensure that the crane system is able to meet the current and anticipated future requirements.
Established in 2011, Avanz Asia Pte Ltd has grown in leadership in the rental industry, leasing, and sales of industrial machinery comprising elevated mobile platforms (MEWP), material handling equipment (MHE), forklift, warehouse equipment and other industrial machinery.
We understand our customer’s business needs and are ready to serve and distribute the machinery equipment and energy-saving tools of international standard quality with world-class products.